💡 The orcuScooter is a project under development. The descriptions on this page represent the current status as well as planned features.
🇺🇸 🇬🇧 An automated software has been used for translatinig the text (German to English) with a few corrections afterwards. I speak English, but I am no native speaker. Please excuse if there are some strange wordings or the like. ➜ Original version (German)
orcuScooter - Recycleable scooter
The orcuScooter is a kick scooter that reinvents the wheel - designed for cycles.
All components can be recycled as many times as needed into new parts - all within one city.
Recyclable plastic parts from the laser cutter, 3D printer and CNC mill. Versatile and reusable aluminum parts.
Clear build and repair instructions and all-bolted construction ensure easy assembly, disassembly, easy repairability and therefore longevity.
Different color and pattern variations and customizable modules make it a long-term companion for young and old, also for schools, companies and clubs.
The scooter is the starting product for a new design concept and the template for many other future products based on this system. The associated production and recycling system is to be realized in a "Fab Factory", a local microfactory with machines for digital manufacturing, in the middle of the city.
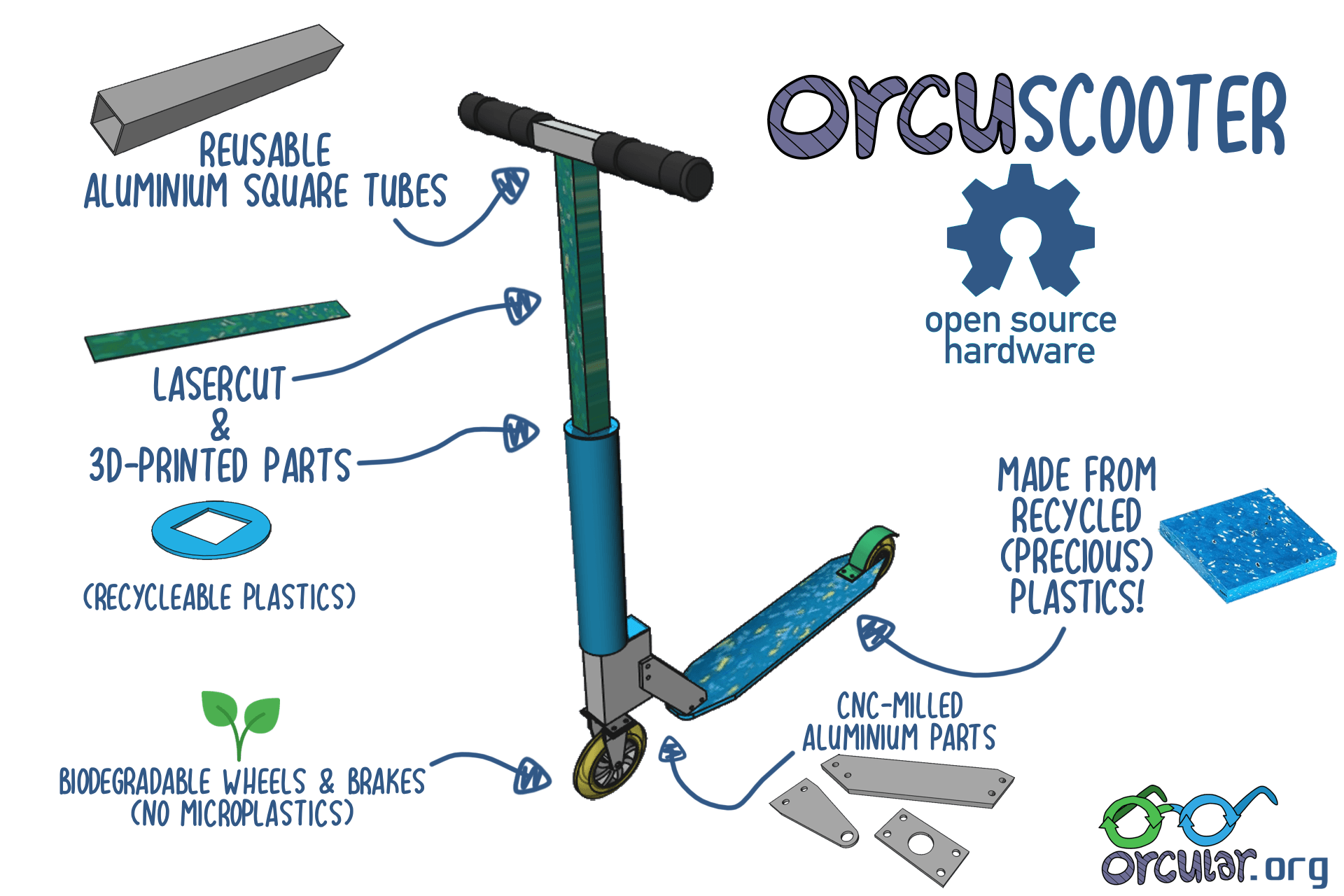
Why a kick scooter?
Admittedly, a kick scooter is not a new invention. However, I was initially interested in creating a product standard and first finding a product in which you find as many different manufacturing processes, materials and design principles as possible combined in one product.
A kick scooter is particularly well suited for this, since it:
- consists of different types of materials
- is manufactured using different fab lab equipment/production processes
- draws attention to the microplastic problem caused by abrasion of tires and brake pads on vehicles and thus offers potential for proposed solutions
Most importantly, a kick scooter is a popular product that numerous children and adults in cities enjoy using for daily transportation. Replacing the many conventionally manufactured kick scooters with sustainable alternatives offers potential for big impact and lots of visibility.
In a nutshell: the problem with today's products
With the orcuScooter project, I want to draw attention to several (environmental) problems and offer solutions.
Many of today's products have the following problems:
- break quickly
- are difficult to repair
- glued and fused parts of different materials (which makes recycling impossible)
- spare parts are often limited or impossible to get
Thus, many products end up in the garbage incinerator or in a landfill abroad and are simply replaced by newly purchased products.
Manufacturing often takes place in faraway countries with questionable environmental and working conditions.
Precious Plastic - why we need to rethink plastic
Plastic has a bad reputation - mostly rightly so. However, plastic is only harmful when it ends up in the ocean or forest, for example. We should also rethink plastic production of new parts from petroleum, because there is already enough of it.
But recycling plastic that already exists, endlessly, into new products over and over again, and preferably larger, fixed components that can't simply end up in the environment - that makes sense. Plastic is precious.
That's why the "Precious Plastic" project (https://preciousplastic.com/), founded in 2013, has developed several open-source machines for plastic recycling, which are also used in the orcuScooter:
In the shredder, old parts, e.g. broken plastic parts of the orcuScooter, are shredded into small pieces. In the sheet press they are pressed into sheets. New parts for the scooters can be cut out by laser cutting or CNC milling. 3D-printed parts made of plastic are also used in the orcuScooter and can be recycled later.
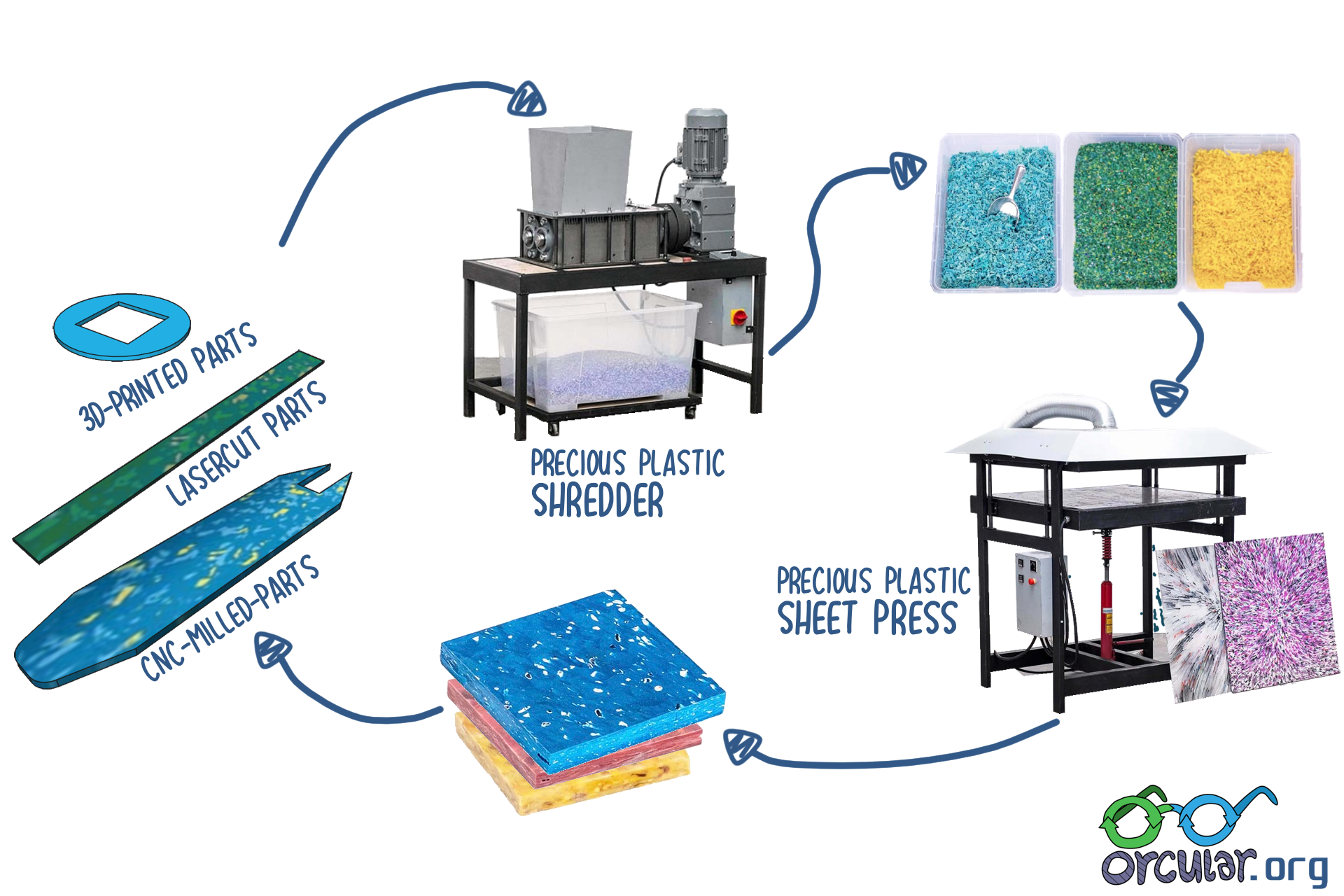
Aluminum parts - Recycle, or better yet: reuse
Some parts should not be made of plastic, as they need higher strength, e.g. the handlebar or reinforcing profiles on the underside of the deck. Several CNC-milled aluminum parts are used, such as connector plates or angles. The steering rod parts are built from square profiles that are cut and drilled to size.
Aluminum is easily recyclable, but the energy required to recycle aluminum is much higher than for plastic. For this reason, aluminum parts of the orcuScooter are initially designed for "reuse", i.e. the parts are designed to be as versatile and reusable as possible - e.g. in new kick scooters or also in cargo bikes from the "Cargo-XYZ" project, from which the design is inspired. The more products that use aluminum square profiles (and there are already many of them), the greater the potential for parts that can be used again and again.
In addition, some aluminum brackets from the "Unipro-Kit" of the Open Source Ecology Germany association are deliberately used. The Unipro-Kit is an open source parts library and offers numerous, very versatile parts. 3D CAD models of all parts are available in FreeCAD format and can thus be easily integrated into the design software.
Customizable versions
Based on the basic version of the orcuScooter, several decorative elements made of plastic plates as well as 3D-printed figures or laser-cut logos are mounted e.g. on the handlebar. Different color and pattern variations and customizable modules make the orcuScooter a long-lasting companion for young and old, also for schools, companies and clubs.
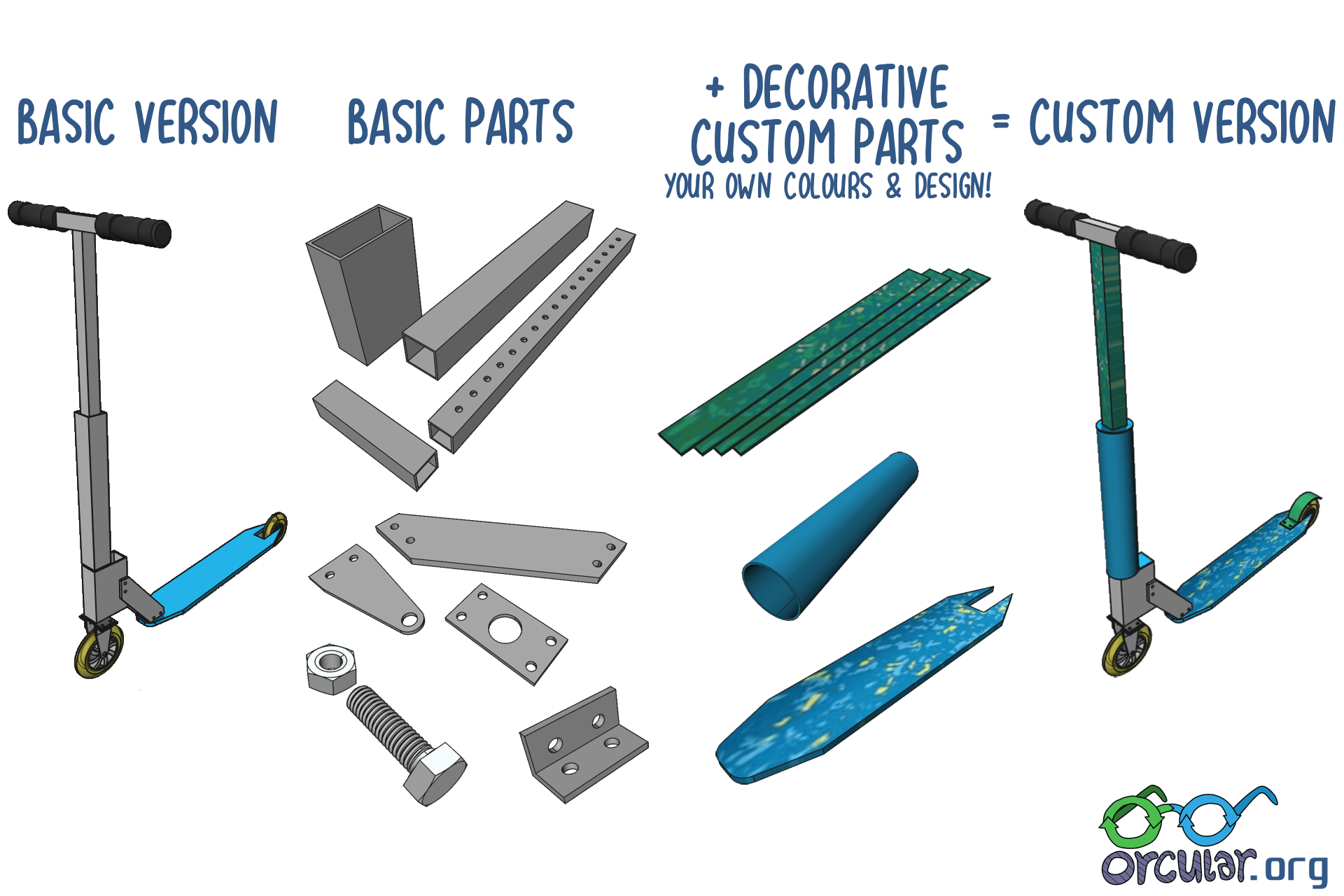
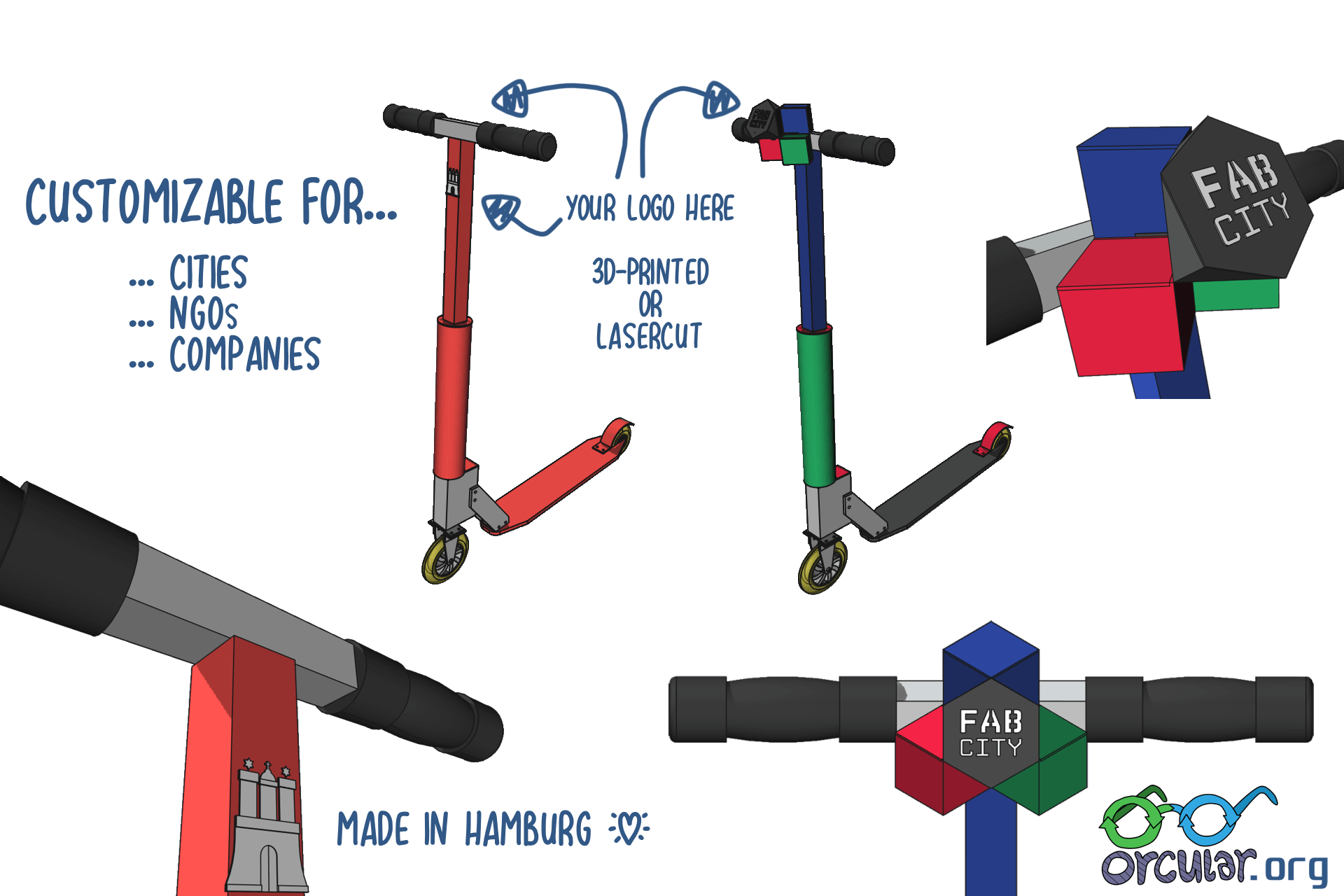
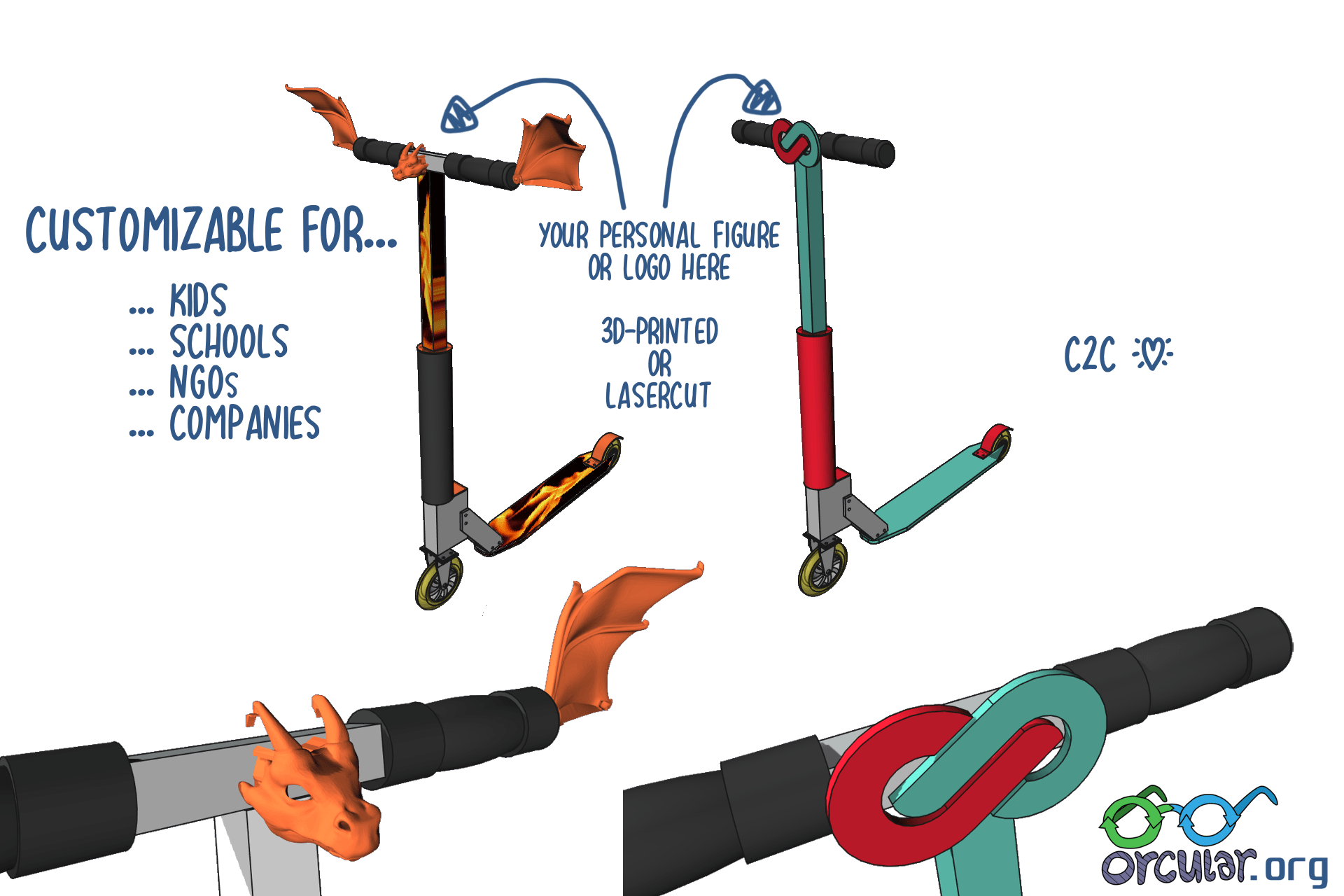
The logos shown in the 3D sketches are merely drafts and suggestions. Actual production and distribution will of course only take place with the prior consent or after order of the relevant institutions to which the logos belonged.
Nature also knows recycling
The orcuScooter was inspired by the Cradle-to-Cradle (C2C) design concept.
C2C distinguishes between two types of cycles:
- the technical cycle for materials such as plastics and metals that are recycled or reused
- the biological cycle for organic materials such as wood and certain textiles and bioplastics.
A major environmental problem is posed by the barely visible microplastic particles caused by abrasion from tires and brakes, for example. Precisely for such wear parts with a lot of abrasion, biodegradable materials should be used as far as possible according to the C2C design concept. For this reason, the outer surfaces of the wheels, the brake pads and the handles of the orcuScooter are made of biodegradable materials - I am currently testing various options for this.
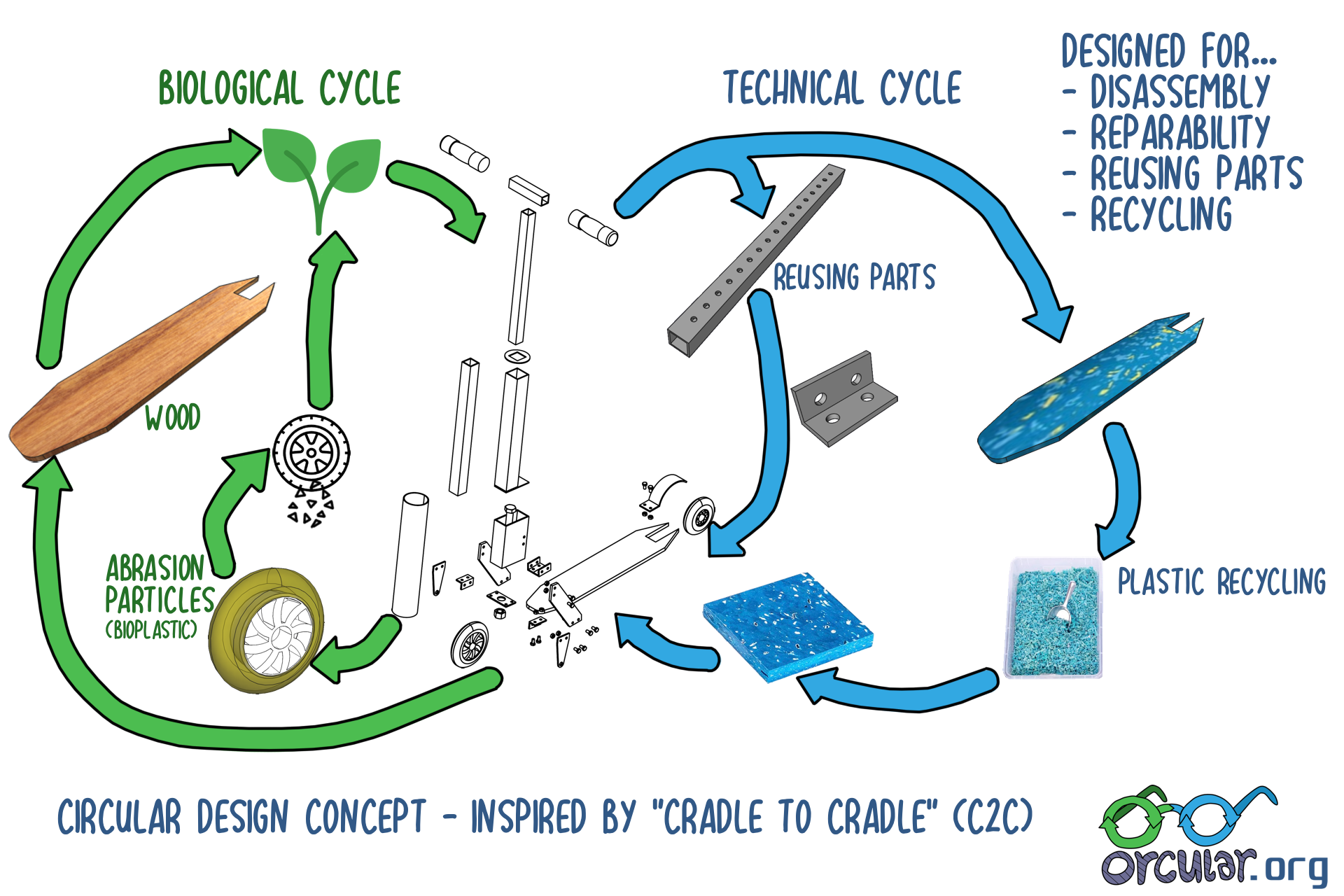
Never miss spare parts again
Many manufacturers don't offer spare parts at all, or if they do, it's often in limited supply and only for a few years. With the orcuScooter this cannot happen: Due to the open-source-available component files, spare parts can be reproduced at will.
You either order them from a company or simply produce them yourself in the nearest fab lab. Over time, new versions of the orcuScooter or individual parts can also be created. Thus, the orcuScooter remains repairable for many years and gets improvements or upgrades over time.
Open Source - in software and hardware
Since the orcuScooter will be published as open source hardware, parts can be easily reproduced anywhere in the world and recycled locally. Also for further development via "distributive design", i.e. by contributions of many different people, more and more improvements, variants and upgrades can be created.
The complete CAD design is done in the free and open source software FreeCAD. This also makes all files created in FreeCAD easily shareable without having to worry about software licenses, cloud constraints, or paid closed file formats.
FreeCAD is a very versatile program, and this project is meant to demonstrate that. Not only did I create the CAD model itself with it, but derived from it I also generate:
- STL files for 3D printers
- Vector graphics for lasercutting
- CAM paths for CNC milling
- Dimensional drawings for handmade parts
- Building instructions in picture and text
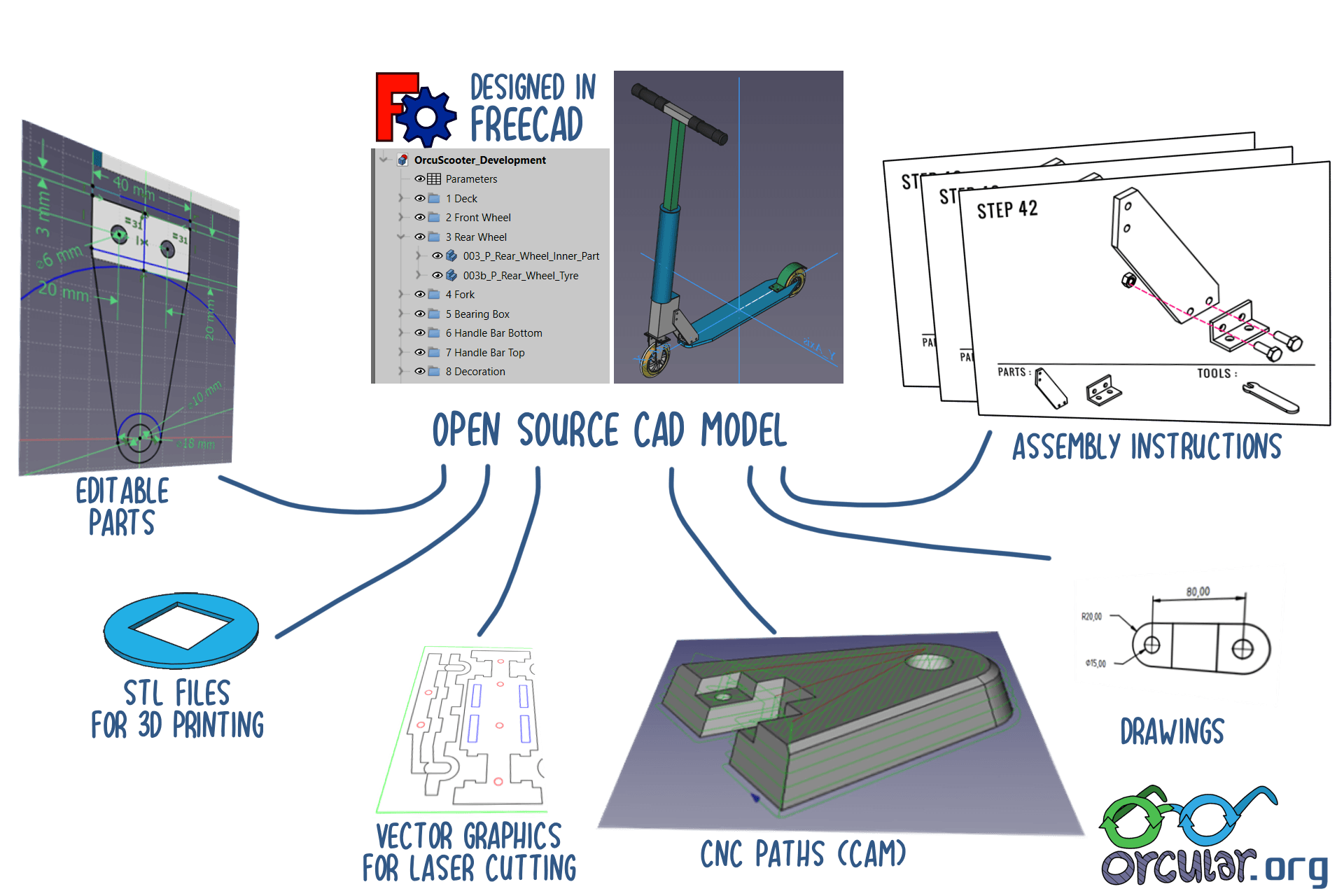
Is this actually an e-scooter?
No, it's a purely mechanical scooter, without an electric motor.
The reasons in a nutshell:
- E-scooters are often not sustainable, they rarely replace car trips, but often replace bike rides and walking trips
- certification and road approval for electric products/vehicles is much more complex
- and above all: one thing at a time ;)
So, if you want to convert or further develop the orcuScooter into an e-scooter after the release - go ahead ;)
Current status & what's next?
I have been working on the scooter project for quite some time. Currently and in the near future, the CAD model will be extended with further details like screw connections, different manufacturing processes will be further tested and optimized (e.g. laser cutting and CNC milling of plastic plates), single parts will be manufactured, assembled and tested.
A first prototype will initially aim to represent a stable and drivable product. In the further process, individual components will then be optimized and additional functions, such as a folding mechanism, will be developed and integrated.
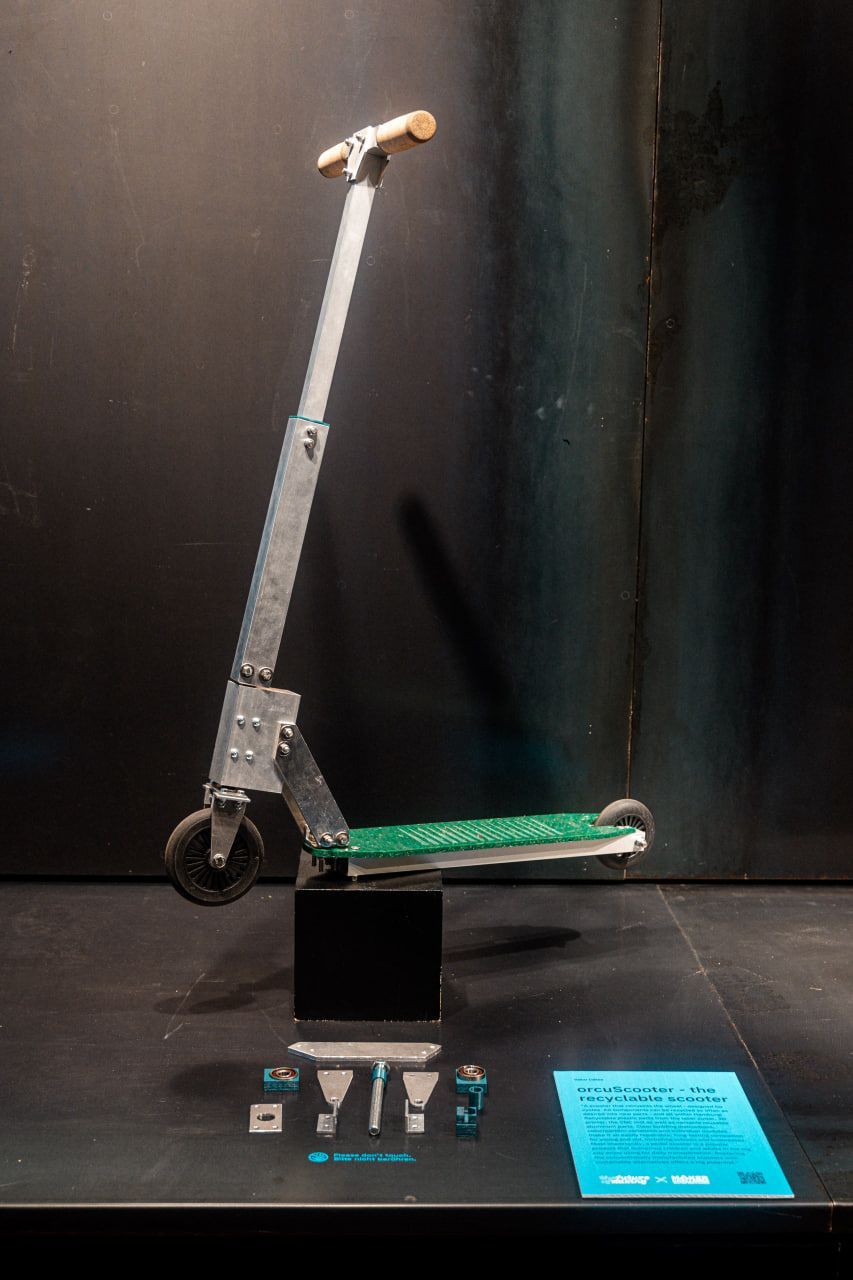
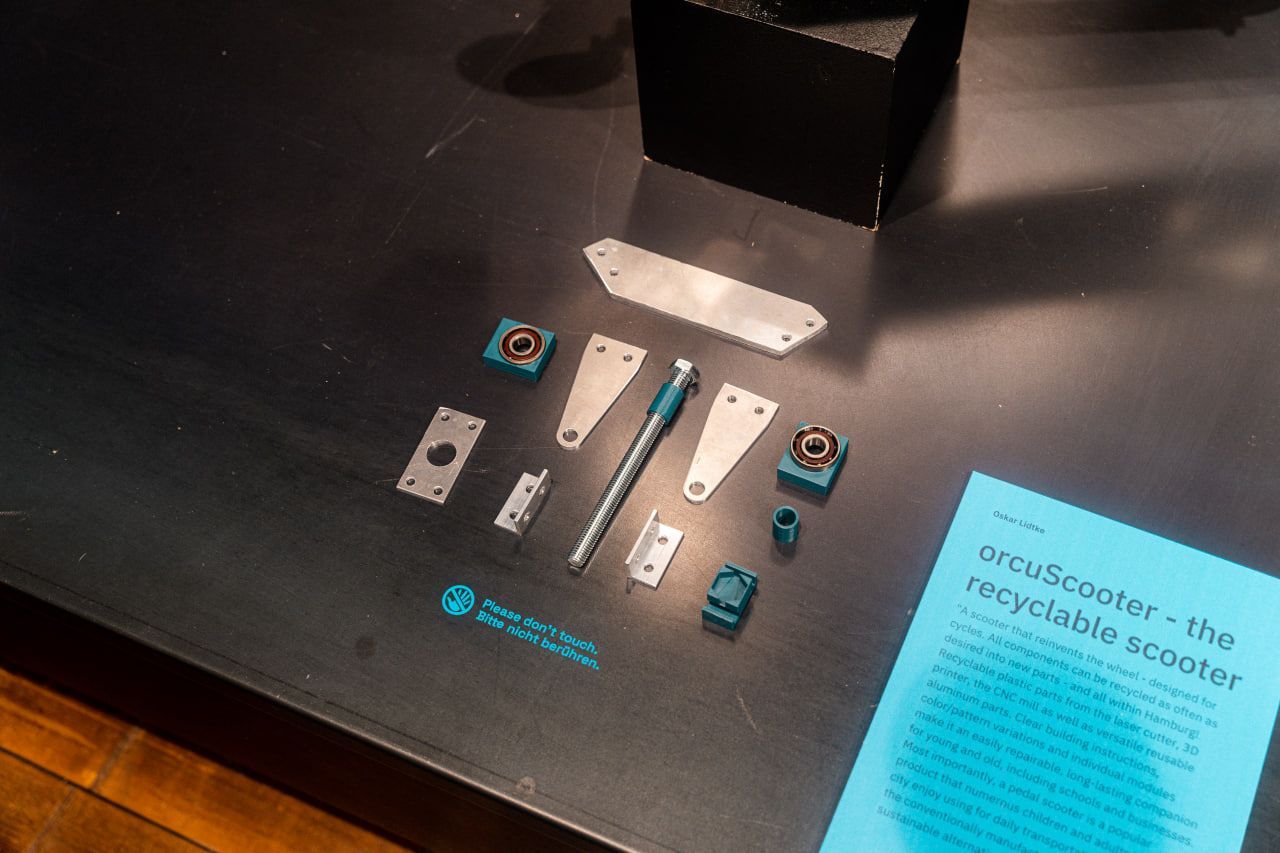
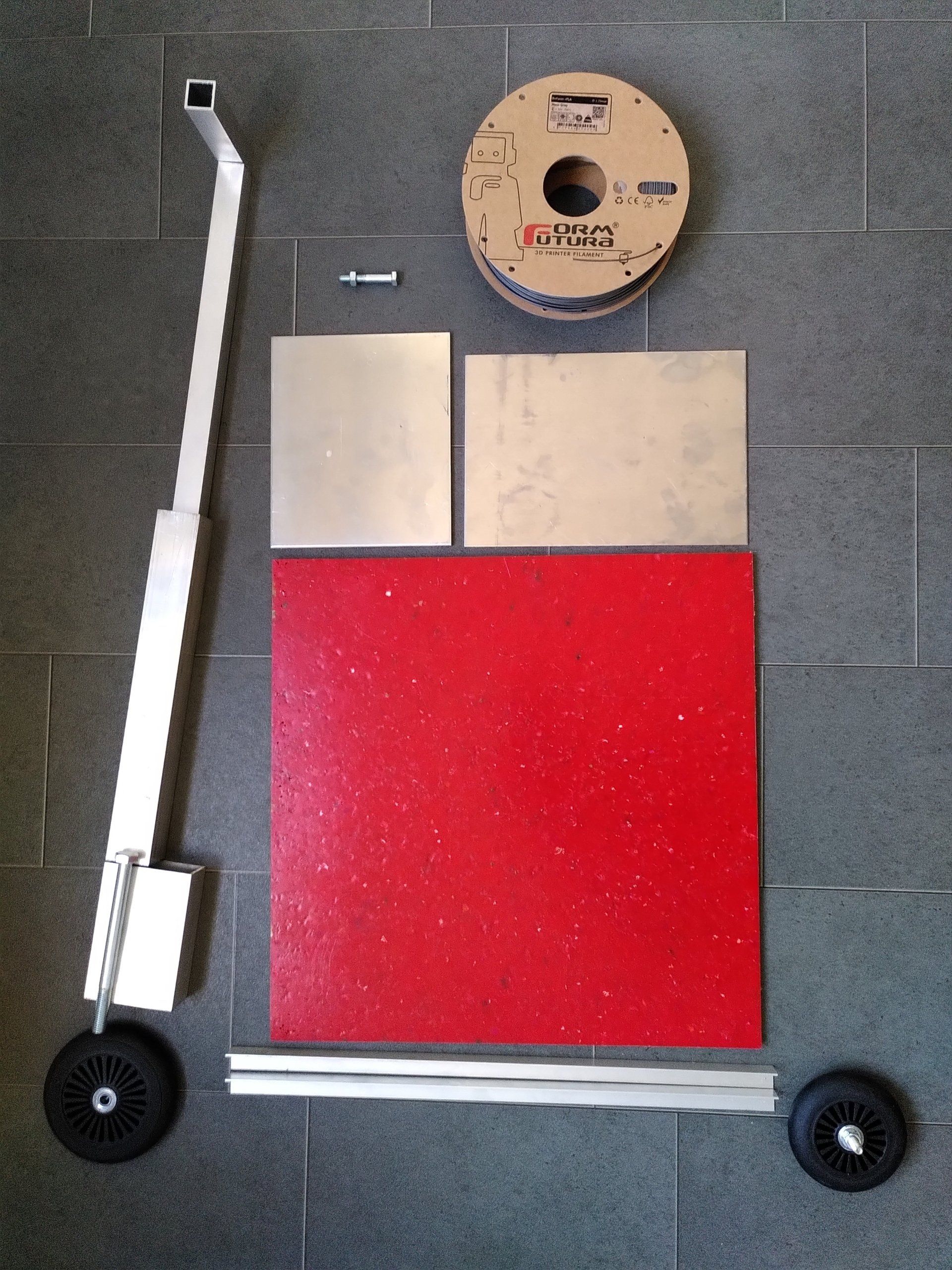
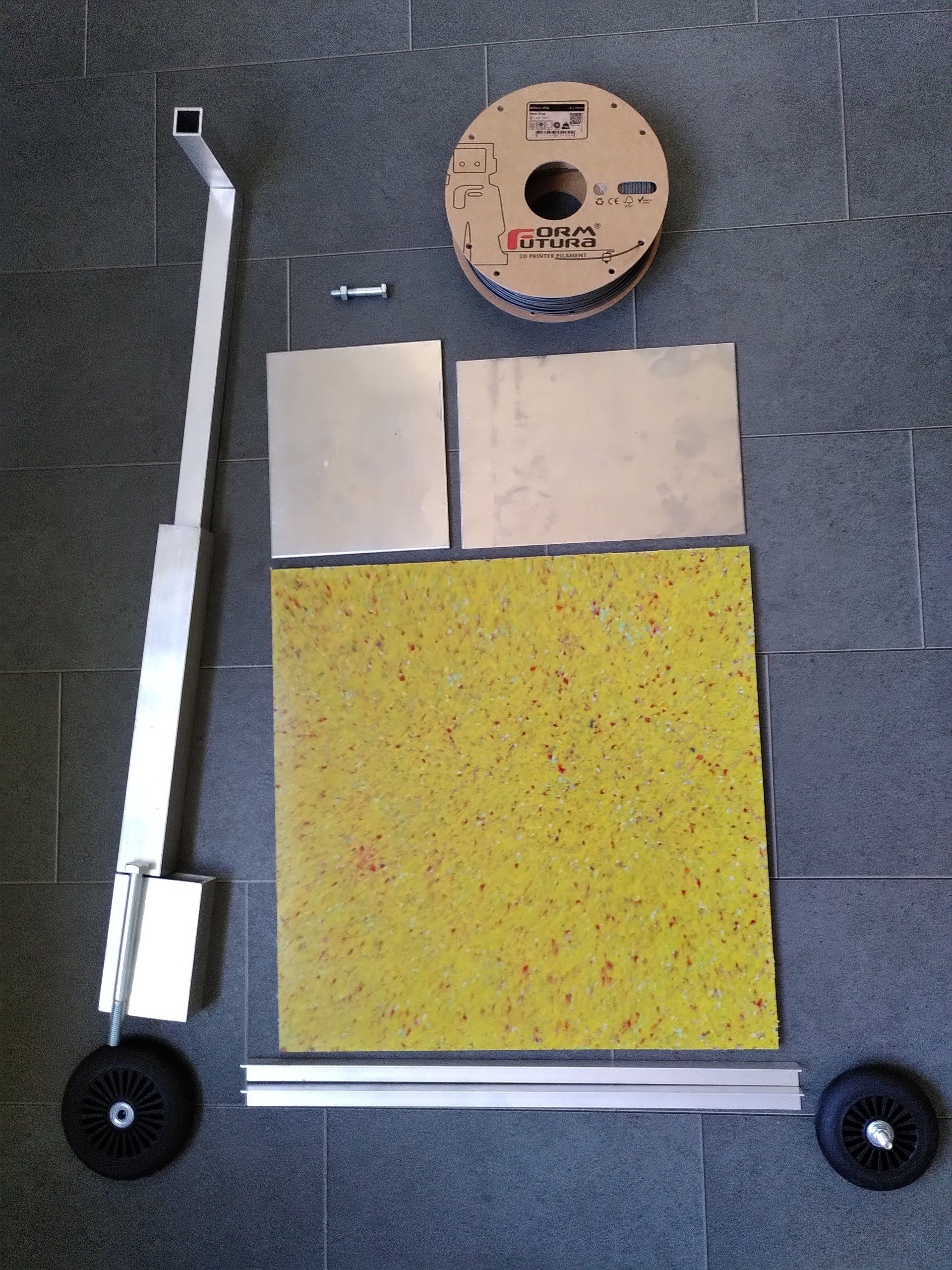
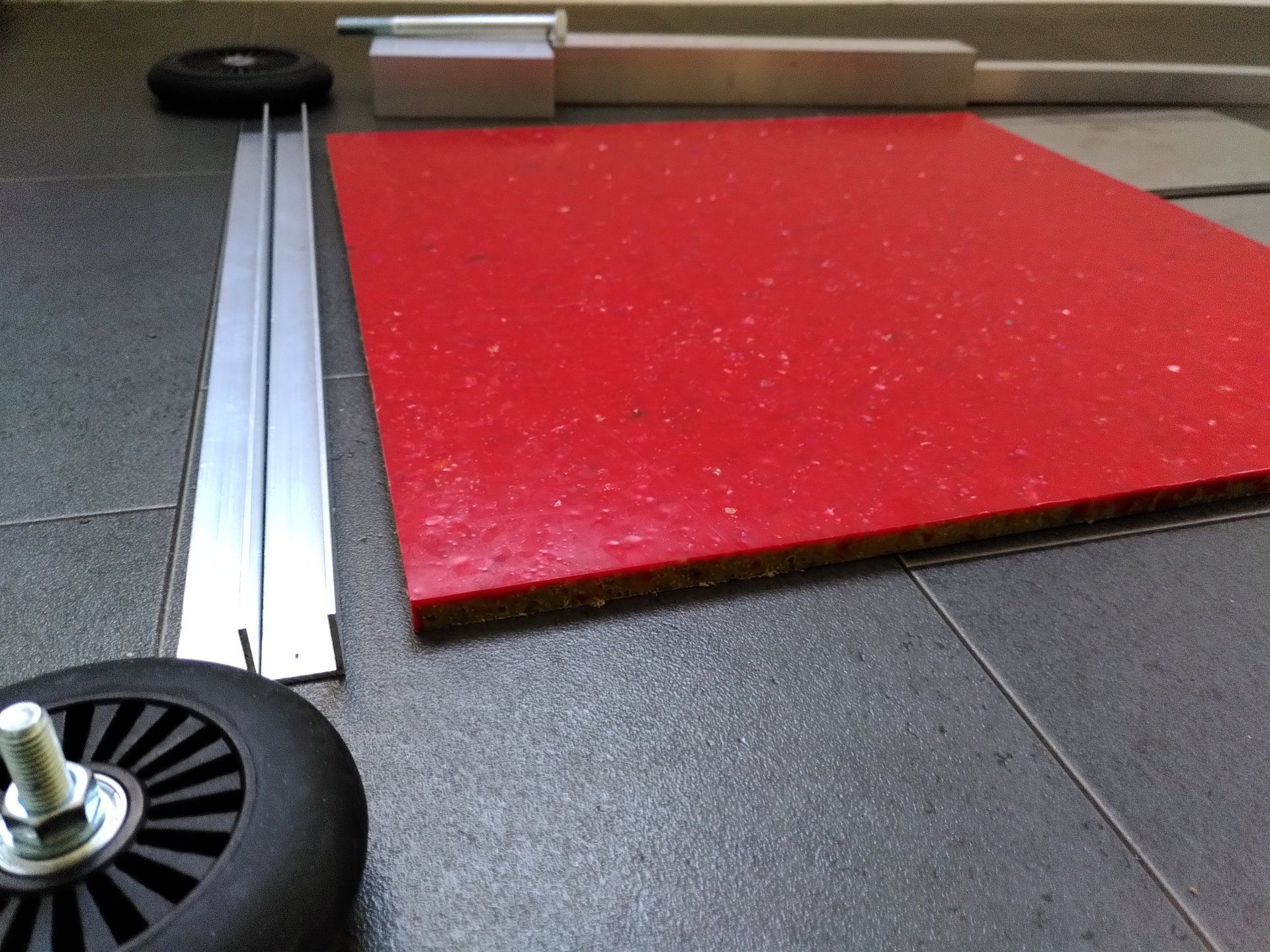
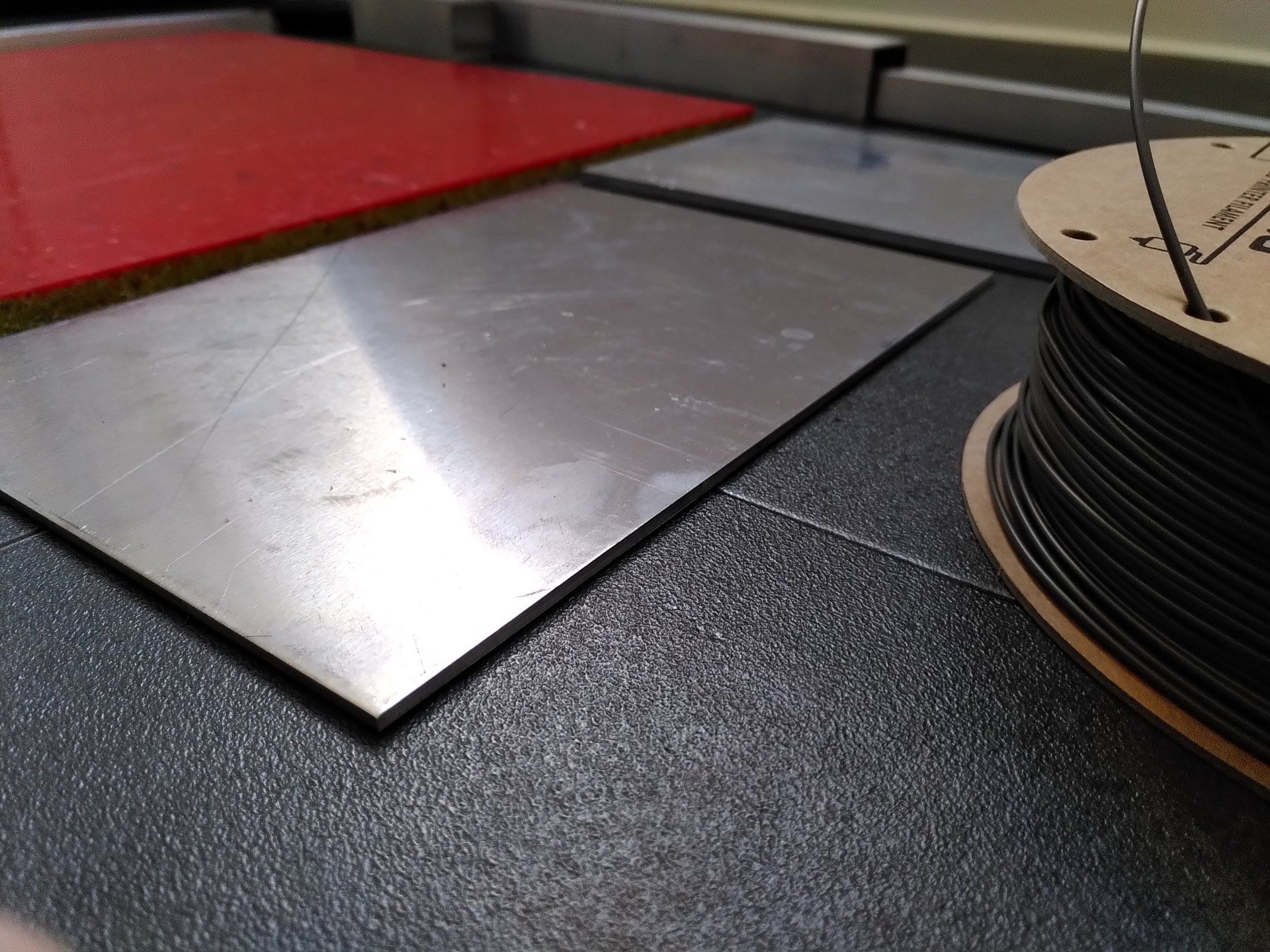
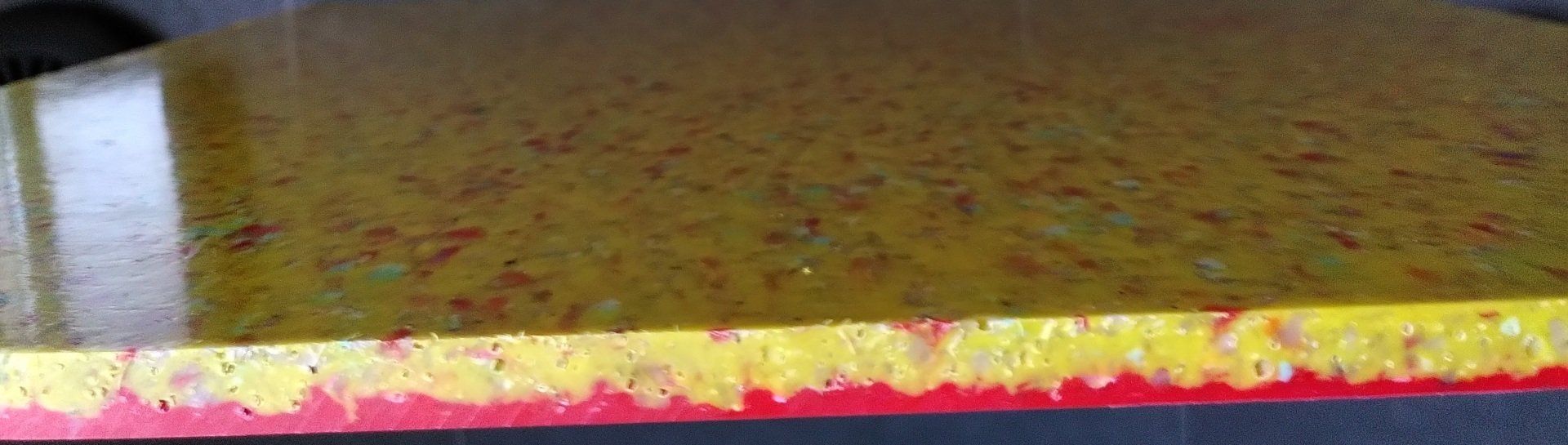
Fab Factory
The whole idea of the orcuScooter and other future products based on this design concept only makes sense with the right production/recycling system and a place to mass-produce and recycle it locally, for the people in your city. My idea of a "Fab Factory" is about setting up a production facility within a city (initially in Hamburg, Germany, where I live) where products can be manufactured using digital production methods (and recycled) in larger quantities.
It is to be a "factory for everything", so to speak, i.e. many different products from just one more or less "universal" production facility. The orcuScooter is to be the first product produced, tested and distributed in the Fab Factory.
It is a longer-term project that is intended to grow slowly. I am applying for funding and searching for other ways to get this place started, hopefully in the near future.
However, starting a Fab Factory is easier than expected: even with one or more 3D printers and a laser cutter, many products can already be produced as construction kits for assembling by the users. In this sense, almost every Fab Lab can already function as a small version of a Fab Factory.
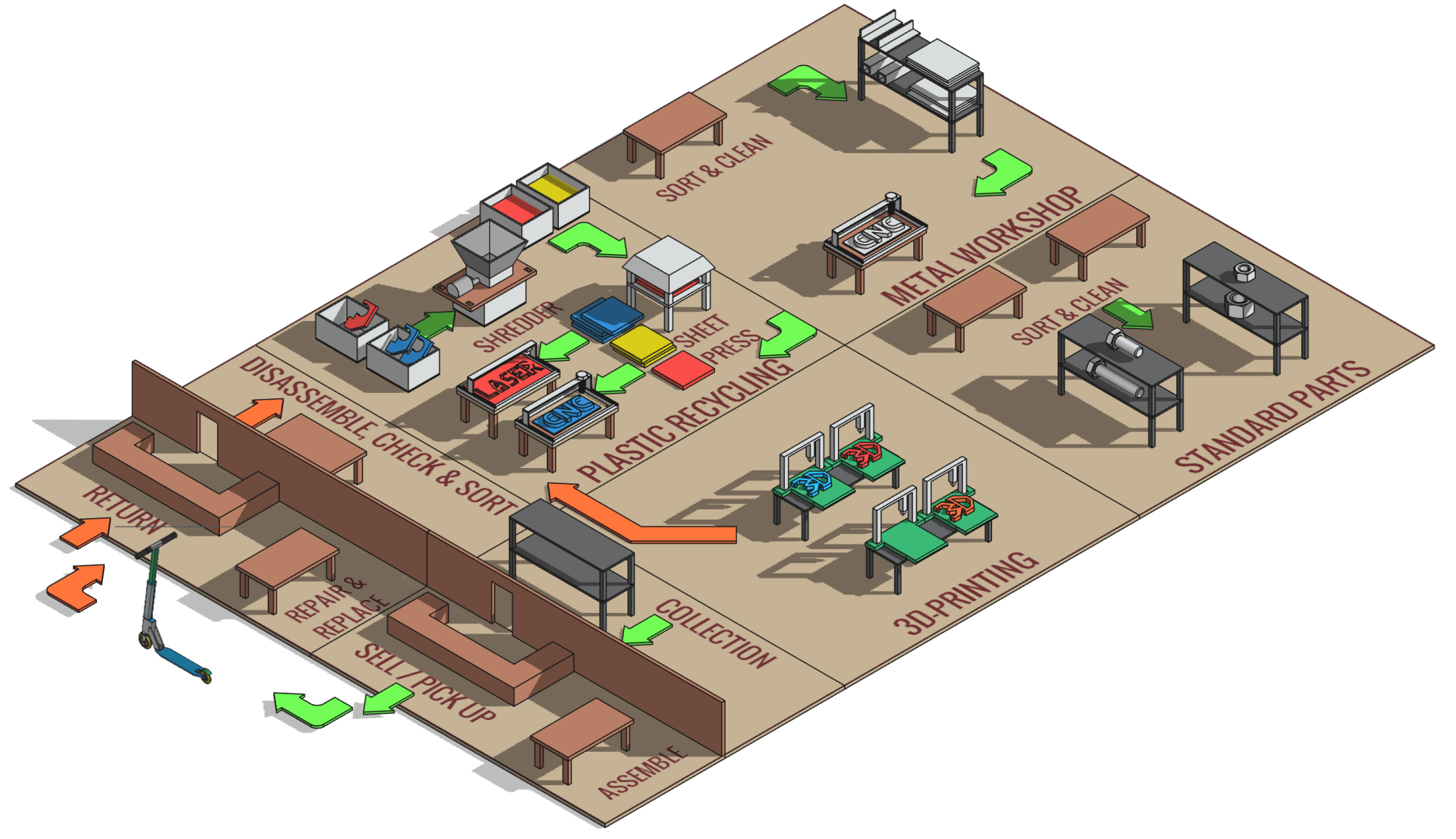
Over time, the goal is to let the Fab Factory grow slowly in terms of:
- Size (e.g. number of 3D printers, growing towards a large printer farm)
- Equipment (start with small, inexpensive devices like 3D printers, later more expensive purchases like professional CNC milling machines)
- Type (initially only production, later also plastic recycling with shredders and plastic sheet presses)
- Degree of automation (initially a lot of manual operation, later software-supported automated processes - from online ordering, to feeding data to manufacturing equipment, to structured collection of orders into boxes)
To facilitate software-supported automation, I am developing a system and already using it in my product designs. This system provides each component with metadata such as material, manufacturing process, color, or even 3D printing-specific parameters such as layer height and links to gcode files.
For a "factory for everything" to be feasible at all, blueprints for many different products are needed first, so the first step is to build the product library, with design contributions from different people and companies. Courses and workshops are also planned.
Above all, it is important that all products are designed according to the same standards and methods which I provide and teach in workshops.
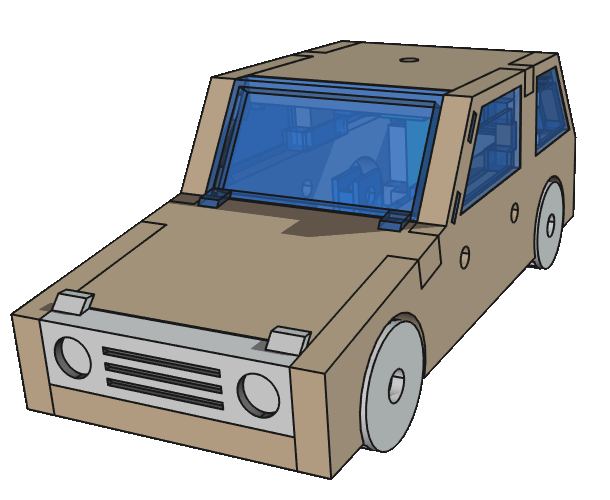
Another project:
orcuCar
A small toy car - as a customizable advertising medium, as a teaching object for design courses or simply for playing.
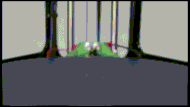
The website is still under construction!
In the not too distant future there will be a lot of news here - get notified 🖂 by email, when it's time ... (only a one-time e-mail, I promise!)